Our Forging
Forging factory
Founded in 1998, a professional IATF 16949 certified manufacturer in Taiwan. Have hot forging, warm forging and combination forging also with the heat treatment and surface treatment under the same roof.
We have 11 production lines with 150 employees and our plant area is 33,060sqm. We are the member of Taiwan Forging Association.
Besides Bicycle, Motorcycle, Railway, Agricultural Machinery, Defense industrial and Security equipment, our main business is automotive parts; automotive parts business accounted for 70%. The main product is automotive suspension control arm for aftermarket (AM), especially for European and America car applications, like Audi/BMW/Mercedes/Fiat/Ford and so on......
Have profound experiences in developing forging mold for automotive parts, especially for suspension control arms. Therefore, we are competent in providing the automotive forging parts with high quality and high stability and have already been audited and approved by several well-known car parts companies.
We provide both steel and aluminum forged control arms using the material same with the original factory (OEM) standard and we control the incoming material by spectrometer.
Although we have run this business for so long, we still keep investing on innovating forging knowledge and technology and new equipment for example Improving production quality and efficiency with the assistance of the Qform/SIMUFACT mold flow software.
The involvement of all team members on the quality control ensures the quality from the raw material coming till the completed parts.
Core Competency
✔ Complex geometry parts
✔ Solution for difficult forging
✔ Rapid tooling development
✔ Engineering for material saving
✔ Skillful technician
✔ Reverse engineering
Forging Manufacturing Capability
✔ Material - Brass, Aluminum, Carbon/Alloy steel
✔ Forging Weight range - 150g to 53Kg
✔ 6 Steel Forging lines (max 5ton)
✔ 6 Aluminum Forging lines (max 4000ton)
✔ 2 Copper Forging lines (max 2500ton)
✔ Heat Treatment - Normalizing, Tempering, T4/T6
Simulation - Mold flow analysis - Die design - Forging - Heat treating - Coining - Tumbling - SandBlasting - Fluorescent/MPI inspection…
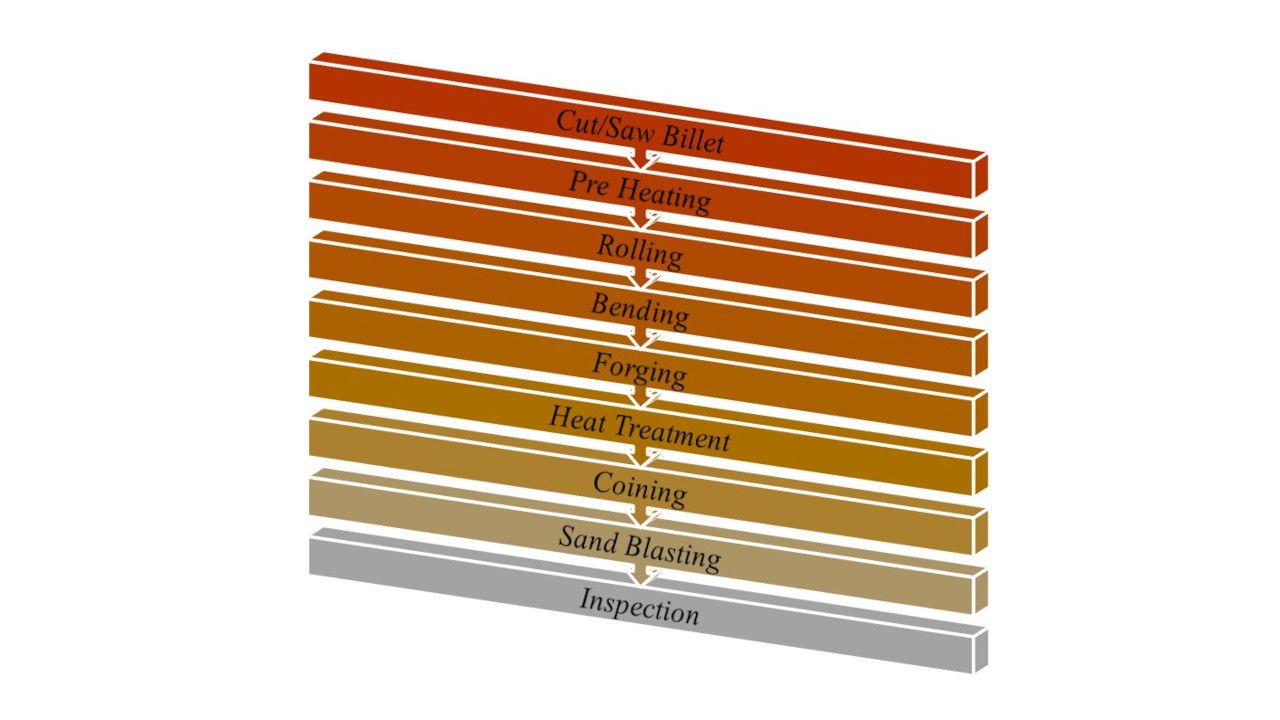
Quality and Manufacturing equipments
# | Process Flow | Aluminum | Steel |
---|---|---|---|
1 | Cut/Saw Billet | Semi-automatic / out sourced | Cutting/Sawing Bed machine |
2 | Pre Heating | Electric Heater *7 | Induction Heater *7 |
3 | Rolling | Horizontal Rolling machine *3 | Horizontal Rolling machine *4 |
4 | Bending | Bending Press *5 | Bending Machine *6 |
5 | Forging | Knuckle Joint Press 650t~4000t *8 Friction Screw Press 2000t *1 | Air Drop Hammer 2.0t~5.0t *5 Crank Press 400t~3000t *5 |
6 | Heat Treatment | T4 Solution Furnace *2 T6 Aging Furnace *2 | NormalizingFurnace *1 |
7 | Coining | Press 650t~1000t | Press 600t~2000t *5 |
8 | Sand Blasting | ShotBlasting Machine *2 | Universal rolling *1 Rack type *1 Barrel type *1 |
9 | Inspection | Rockwell Hardness Meter CMM Universal Test Machine Magnetic Particle Inspection Machine Semi-automatic Fluorescent Inspection Spectrometer Metallographic Microscope Reverse Engineering Scanner |
- ISO 9001 Certification
- IATF 16949 Certification
- Metallographic analysis
- Reverse Engineering Scanner
- Universal Testing
- CMM
- Operation Quality Control
- Magnetic Particle Inspection
Press Release
- BMW 7 Series E38
Full set suspension control arm products, 7 series, E38 1995 ~ 2001.
Read More - BMW 5 Series F10
Full set suspension control arm products, 5 series, F10 2010~, 6 series. F06 2010~
Read More - Mercedes Benz S-Class
Full set suspension control arm products, S-Class W211 2002 ~ 2009.
Read More